Industrial Automation
Individual life-cycle record for every tool
Tools such as drills, milling machines, or planes are currently replaced or reground on a regular basis – a high-maintenance and cost-intensive process. Researchers from Fraunhofer IMS are now working on a more efficient solution. Using an individual “life-cycle record” for tools and a new transmission technology by means of an RFID tag, they intend to optimize the productivity, quality, throughput time, and stock of manufacturing businesses in the Industry 4.0 age.
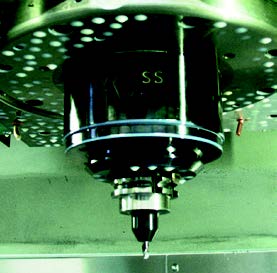
Work steps such as drilling, milling, turning, or planing do leave their mark on the tools used and, over time, lead to wear and tear. The service life determines when the time has arrived to replace or re-grind the tool. Due to the varying effects on a tool while it is being used, however, this time is very difficult to determine exactly. Tool characteristics can be calculated, but the machine setting is usually made by an employee, which represents an untraceable influence on the machine in question. In order to avoid downtime and damage to workpieces, tools are therefore often replaced too quickly. This may result in additional costs of up to 50 %.
RFID tag allows interruption-free operation
To ensure that maintenance or replacement does not take place until necessary, however, many specific factors would have to be taken into account, such as the cutting task in question, the machine settings made by employees, or the material that the workpieces are made of. The solution: an individual life-cycle record that contains every event in the life of a tool. Based on this data, a special management tool then creates a digital tool twin that can be used to precisely determine when a tool should be replaced or repaired. In order to transmit the “real” data from the tool to the management tool, researchers at the Fraunhofer Institute for Microelectronic Circuits and Systems IMS have chosen RFID technology. As part of the “Cute Machining” project, they have developed new transponders that work in a frequency range of 5.8 GHz and that can be read from a distance of one meter, even in the difficult metallic environment of production facilities. Because the RFID transponder takes up less than 5 mm², it can be easily installed on a tool’s surface.
New applications for Industry 4.0
Manufacturing companies benefit from this technology not only because their tools are used to optimum capacity. By capturing the most comprehensive data possible from the production environment, companies are able to create a transparent and more efficient production process – a central aspect of the path towards Industry 4.0. The first step the new technology takes is to identify the tool. Later on in the project, however, the sensors could also be used to supply not just tool-related data, but also information about the environment in which the tool is used. But this technology could also be used in other areas of Industry 4.0. For example, all “assets” on the lower physical levels, such as tools, workpieces, machines, or vehicles, could be fitted with RFID tags in order to gain an even wider range of information. This information could then be used to identify more potential for optimization.
About the project:
The project consortium comprises, in addition to Fraunhofer IMS, the technology companies CIMSOURCE GmbH and PROMETEC Gesellschaft für Produktions- Mess- und Automatisierungstechnik mbH, ID4US GmbH, the Heinz Nixdorf Institute at the University of Paderborn and the application partner Sandvik Coromant Deutschland. “Cute Machining” is funded by the state government of North Rhine-Westphalia and the EU as part of the EFRE-NRW program.
Last modified: