Etching expert at Fraunhofer ISIT
Oxidizing, etching, structuring, polishing and depositing are part of Dr. Marie Christin Wolff’s everyday work. At Fraunhofer ISIT, she and her team are dealing with single process development in the fields of wet chemistry, electroplating and chemical mechanical polishing (CMP).

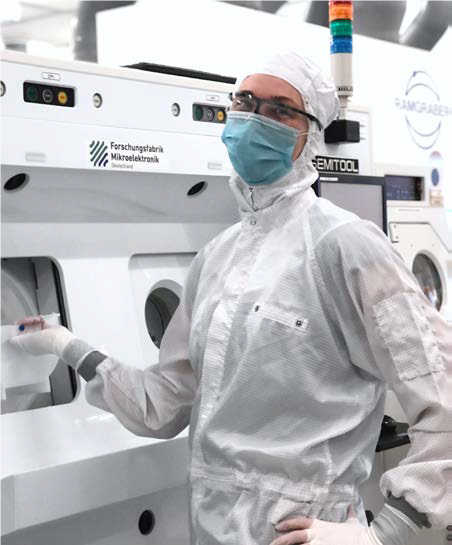
Dr. Wolff, what are you and your team working on right now?
We manufacture microsystems. My team and I develop the individual processes for planned components and take care of process stability and the associated equipment. We work on pretty much all processes that have something to do with (corrosive) liquids – that is more or less the common denominator of the team. This includes electrochemical deposition processes in electroplating, but also chemical-mechanical polishing of wafer surfaces. In between, there are all the etching and cleaning processes in wet chemistry. Within the Research Fab Microelectronics Germany and the Fraunhofer Group for Microelectronics, we are currently involved in expert groups to strengthen the shared experience of those responsible for devices. This results in good networks and exchange platforms. We can show customers from this pool a second supplier for processes, offer completely different processes or stimulate expert discussions on process control.
What is your work useful for?
The results of our work are a central component for the production of MEMS components and MEMS devices. In Fraunhofer ISIT’s 1000 m² clean room, wet chemistry, electroplating and CMP make an important contribution to the process chain to realize sensors, actuators and post-CMOS integration. For example, we etch electrode structures and membranes, deposit conductive tracks and pads, and polish glass and metal surfaces.
What is the share of microelectronics in your research area?
If you look at the chain of creating components, we are part of the manufacturing. In our daily work, we apply our processes to different materials and stacks. One of our main tasks is to integrate and evaluate materials that are new to us into our existing equipment, such as aluminum scandium nitride, parylene or gallium nitride. But also the testing of other etching media, grinding materials or electrolytes is part of it. The balancing act is to make the processes as comparable and reproducible as possible despite the different substrates. At the same time, the different requirements of a feasibility study have to be combined with pilot production and, in some cases, production on the same equipment.
What do you find particularly exciting about your work?
I like the combination of practical relevance and the freedom that comes with a research environment best. In addition, I haven’t been in the cosmos of microelectronics and silicon technology for that long, so every new project is exciting for me.
Dr. Marie Christin Wolff studied chemistry at the University of Oldenburg and subsequently completed her doctorate in inorganic chemistry at the University of Hamburg in AK Heck. In 2018, she moved to the Fraunhofer Institute for Silicon Technology ISIT, where she first worked in the area of electroplating and then also in the area of wet chemistry. In January 2020, she became team leader of the fabrication for wet chemistry, electroplating and chemical-mechanical polishing. Since summer 2020, Dr. Wolff has represented Fraunhofer ISIT on the Scientific and Technical Council of the Fraunhofer-Gesellschaft.
Last modified: